Project description
One of RazorEdge’s customers runs a facility that has multiple production lines consisting of multiple devices that need to be configured based upon the product they are producing. The previous method required an operator to manually configure every device upon startup, which can cause issues with the finished product if any one of the devices is configured incorrectly. Outside of the opportunity for errors, the time it would take to set up the line for each job could be anywhere from 15 – 20 minutes which adds up to many hours when there are many product changes.
Aside from trying to minimize errors, and improving the efficiency of starting the line, another requirement was to be able to capture the data from the various devices in order to report key metrics, on line performance, and product quality.
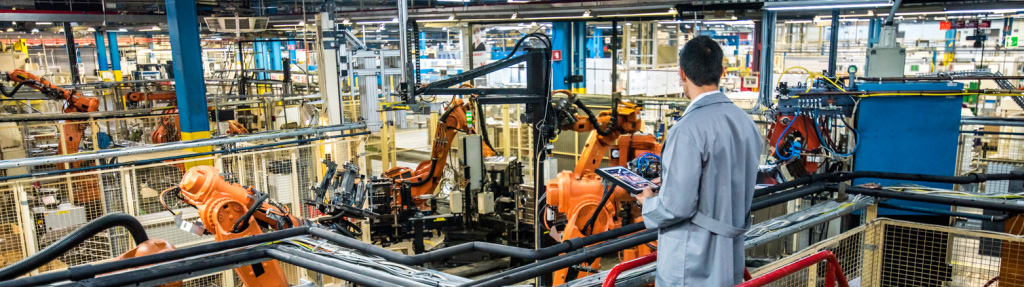
Solution
The perfect solution for this scenario was Open Automation Software with a native PLC drivers, Universal Driver Interface (UDI) for custom protocols, Data Route functionality, and .NET Integration. The two major devices that needed attention on were an Allen Bradley PLC, and a Zumbach Electronics diameter monitor.
OAS with its built in Allen Bradley drivers made the communication to the PLC a breeze. Communicating with the Zumbach required the creation of a Universal Driver Interface to send and receive ASCII commands to the device to control and retrieve information using their Host Protocol.
Basic Process
Product Setup
Administrators access a web portal (Microsoft MVC application) to set up the parameters for every device/part number that they produce. This includes line parameters such as target line speeds, specification ranges for bare and finished product, and various other setup information.
Starting the job
Jobs are scheduled by a dispatcher to fulfill orders, and that list of orders is displayed on a Windows Desktop application. The operator then chooses which order they are about to run by hitting a “Start Job” in the app. The .NET service loops through every device setup for that particular line and using the OPCSystemsData component sends the appropriate values to tags that have been created for each device.
Custom Protocol with the UDI
In order to communicate with the Zumbach controller, RazorEdge decided on using a custom UDI which would use the Zumbach ASCII Host Protocol to send and receive data to the device. When the start job method writes to the value of the “Activate Product” tag, UDI sends the appropriate ASCII strings to load the product from the local device tables, verify the information, and Activate the recipe.
The UDI SDK handles all of the communication of data between the data source and the OAS Platform, which can then be used just like data from a native PLC driver. The only requirement was writing code to handle the Zumbach ASCII protocol within .NET code.
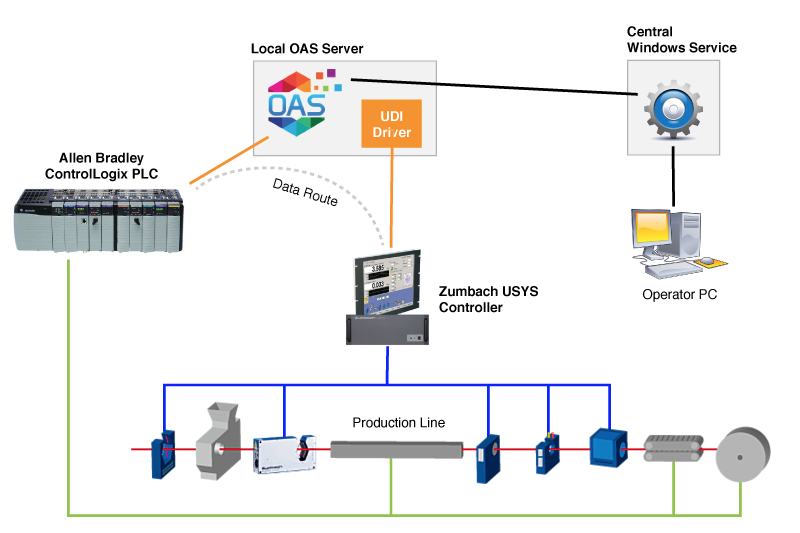
Data Translation with Data Route
Using the Data Route feature of the OAS Platform, it was then possible to translate data from the Zumbach Controller into the Allen Bradley PLC. This capability of the Platform is available for any data exposed to the OAS service, effectively making it a universal data bus.
Outcome
With the utilization of OAS, RazorEdge was able to successfully implement an automated startup configuration for each device on the line. They have improved startup times, minimized errors, and provided a foundation for getting critical operating data to feed their data analytics systems to provide Overall Equipment Effectiveness data.
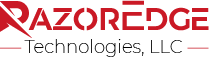
Visit https://razoredgetech.com/ for more information on RazorEdge Technologies, LLC and services they provide.