Summary:
- Industry 4.0 integrates digital technologies into manufacturing, creating smart factories.
- Key technologies include IoT, AI, cloud computing, and 3D printing.
- Benefits: increased efficiency, reduced costs, improved quality, and faster time to market.
- Real-world applications: predictive maintenance, smart factories, and personalized manufacturing.
- Embracing Industry 4.0 is crucial for staying competitive.
Manufacturing is always evolving. From steam engines to mass production, each industrial revolution has reshaped how we create and distribute goods. Now, we’re entering a new era—Industry 4.0. But what is Industry 4.0?
In this post, we’ll break down the key components, benefits, and real-world applications of Industry 4.0.
What is Industry 4.0?
Also known as the Fourth Industrial Revolution, Industry 4.0 is the transformation of traditional manufacturing through digital integration.
At its core, Industry 4.0 creates “smart factories” where machines, systems, and products communicate, generating data to optimize efficiency and drive innovation. This is made possible by several key technologies:
IoT & IIoT
Connecting industrial equipment, sensors, and systems to the Internet enables real-time data collection, remote monitoring, and process control. Think of sensors on a production line feeding data to a central system for analysis. That’s the power of IoT connection and IIoT industry 4.0 in action.
Cyber-Physical Systems (CPS)
These bridge the physical and digital worlds by integrating machines with software, sensors, and network connectivity, allowing real-time monitoring and control.
AI & Machine Learning
With so much data being generated, AI and machine learning analyze patterns, predict failures, optimize processes, and even automate decision-making to boost efficiency.
Cloud Computing
Cloud-based platforms provide scalable storage and processing power, enabling manufacturers to leverage advanced tools without heavy hardware investments.
Big Data Analytics
Industry 4.0 generates massive datasets. Advanced analytics tools extract valuable insights to improve production, quality control, and supply chain management.
Additive Manufacturing (3D Printing)
3D printing allows for rapid prototyping and on-demand production, offering flexibility and customization in manufacturing.
AR & VR
Augmented and virtual reality enhance training, design, and process optimization by overlaying digital information in real-world applications or creating immersive simulations.
Benefits of Industry 4.0 Manufacturing
Industry 4.0 isn’t just about flashy new tech. It delivers real, measurable benefits for manufacturers. Embracing it means a stronger, more competitive business. Here’s how:
Increased Efficiency and Productivity
Automation, real-time data, and smarter workflows define Industry 4.0. By connecting machines and systems, manufacturers get a clearer view of their operations, making it easier to:
- Identify bottlenecks
- Streamline processes
- Automate tasks
This results in a big boost in efficiency and productivity. Think of production lines that adjust themselves in real-time, cutting downtime and maximizing output.
Reduced Costs
The efficiencies gained through Industry 4.0 can lead to cost savings. Better resource use, predictive maintenance, and less downtime all help cut operational expenses.
With IIoT-driven predictive maintenance, manufacturers can catch equipment issues before they become costly breakdowns, reducing unexpected downtime and repair costs.
Better Product Quality
With smarter monitoring, data analysis, and process control, manufacturers can improve product quality across the board. Real-time sensor data helps catch and fix defects early, reducing waste and keeping quality consistent.
AI-powered vision systems take it even further, spotting tiny imperfections so only top-tier products make it to market.
More Flexibility & Agility
With Industry 4.0, adaptable production and customized products are easier than ever. Connected systems help manufacturers quickly adjust to shifting customer demands and market trends.
3D printing takes it a step further, enabling on-demand production and opening the door to more personalized products.
Faster Time to Market
Smoother workflows and rapid prototyping help get products out faster.
Digital twins, virtual models of real products and processes, let manufacturers test and refine designs before making physical prototypes. This shortens development cycles and speeds up time to market.
Improved Safety
Smarter monitoring and risk management help create safer work environments. Sensors can spot hazards, and connected systems can shut down equipment automatically in emergencies.
AR and VR also play a role by offering realistic safety training to reduce workplace accidents.
Data-Driven Decision Making
Industry 4.0 gives manufacturers access to tons of data, helping them make better business decisions.
Real-time dashboards keep managers updated on production performance, making it easier to spot trends, adjust strategies, and optimize operations on the fly.
Investing in Industry 4.0 can pay off in a big way. While there’s an upfront cost for technology and infrastructure, the long-term benefits make it a smart move for manufacturers looking to stay competitive in today’s global market.
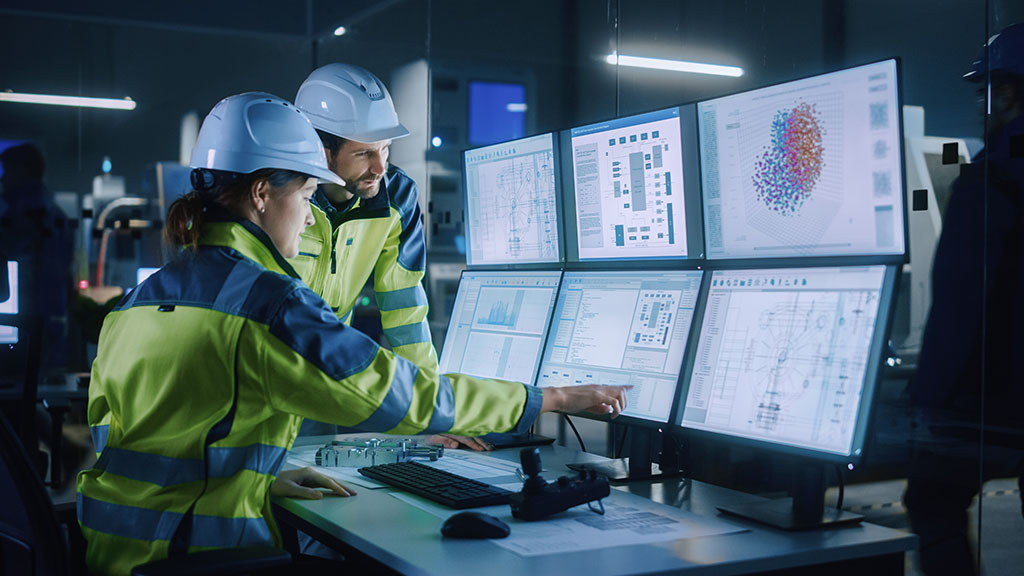
Real-World Applications
Industry 4.0 isn’t just a concept; it’s already transforming manufacturing. Here’s how:
Predictive Maintenance
Instead of waiting for equipment to fail, sensors track real-time data like temperature and vibration. AI analyzes this data to predict issues before they happen, allowing for proactive repairs that reduce downtime and costs.
Smart Factories
Fully connected, automated facilities use AI to optimize production, adjust schedules based on demand, and even reconfigure assembly lines in the moment. Data flows seamlessly across systems, improving efficiency at every level.
Supply Chain Optimization
Real-time tracking of materials and shipments keeps supply chains running smoothly.
Automated systems can adjust inventory based on demand, ensuring products are always available without overstocking.
Personalized Manufacturing
Industry 4.0 makes mass customization possible.
3D printing and data analytics allow companies to create made-to-order products, from custom-fit shoes to cars tailored to individual preferences.
Advanced Quality Control
AI-powered vision systems catch defects in real time, spotting issues human inspectors might miss. This means fewer production errors, less waste, and consistently high-quality products.
These examples show how Industry 4.0 is already making a difference. As technology advances, even more innovative applications will emerge. The bottom line? Industry 4.0 isn’t the future—it’s happening now.
Embracing the Transformation
From IIoT connectivity to AI-driven insights, Industry 4.0 is transforming factories, supply chains, and entire industries. Embracing it is no longer optional; it’s essential for staying competitive in today’s fast-changing world. The potential of Industrialization 4.0 is big, and the journey has only just begun.
Ready to enhance your manufacturing with Industry 4.0? Open Automation Software provides a seamless platform to integrate, visualize, and manage your industrial data. Explore our solutions and see how they can power your Industry 4.0 initiatives.
Request a free demo today and discover how we can revolutionize your operations.