Summary:
SCADA is a large-scale system for monitoring, analyzing, and controlling industrial processes, while HMI provides local control over individual machines. HMI is a subset of SCADA, offering a user interface for operators. SCADA enables remote control and data analysis across operations. Try the OAS Platform for advanced automation solutions.
SCADA and HMI are closely connected systems that enable efficient and productive industrial automation.
Supervisory control and data acquisition (SCADA) systems and human-machine interface (HMI) systems play complementary roles but are also clearly distinct and fulfill different specific purposes.
So, what sets HMI and SCADA apart? What are the differences between the two, and how do they work together? First, we’ll review what HMI and SCADA are. Then we’ll move into a comparison of HMI vs SCADA.
What is SCADA?
In industrial automation, SCADA is a large-scale control system architecture. It includes a wide range of hardware and software elements, from programmable logic controllers (PLCs) and remote terminal units (RTUs) to sensors and peripheral devices.
The overall intent of these systems is to monitor, oversee, and control industrial and manufacturing processes both locally and remotely. SCADA systems allow users to directly interact with machines and other physical assets as well as collect data from them for log-keeping, reporting, and more.
In the SCADA vs HMI discussion, it’s especially important to remember that SCADA is the “big-picture” system. It allows for an overview of and control of individual units within an entire industrial or manufacturing operation.
The SCADA system can deliver alerts when parts of the system are operating outside of set parameters, allow remote users to make adjustments or pause production, and much more. These systems can manage advanced control strategies and other complex, system-wide actions, as Automation Community explains.
The data analysis element of SCADA shouldn’t be overlooked. The scale at which these systems operate allows users to see the entirety of operations, the larger processes that are made up of several smaller and distinct workflows. By collecting, analyzing, and visualizing relevant data, SCADA software empowers high-level insight and targeted improvement.
There are several elements of a complete SCADA system. These range from the inputs and sensors that transmit raw data from individual parts of the system to the PLCs and RTUs that gather this data, convert it into a format that’s easier for operators to understand, and help to control individual pieces of machinery and equipment in the network.
HMI software is another key part of the overarching SCADA system. In short, HMI systems are displays – often but not always graphical user interfaces (GUIs) or physical control panels – that control specific pieces of equipment and machinery. Let’s take a closer look at HMI.
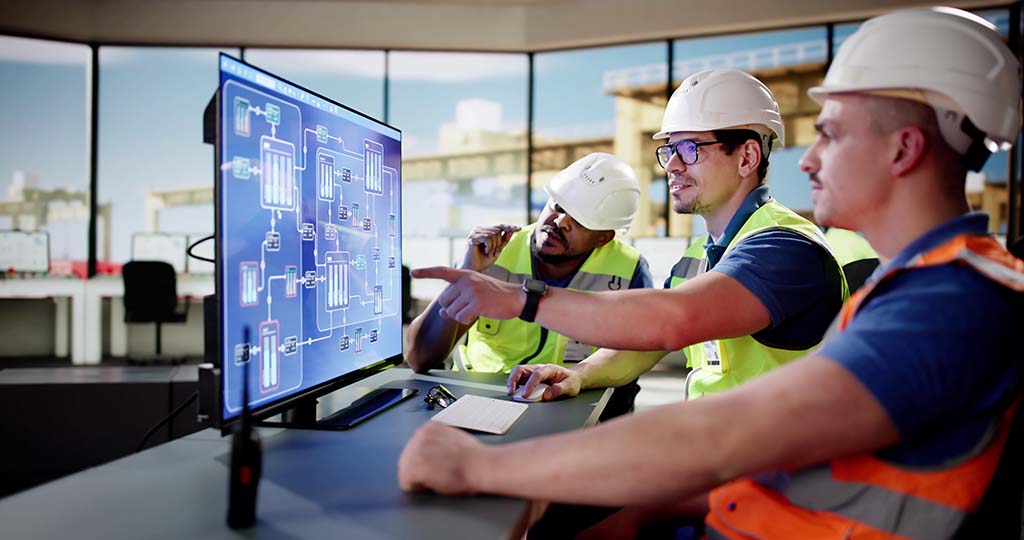
What is HMI?
HMI refers to the human-machine interface, a broad term that refers to the systems and controls that humans use to control and otherwise interact with a given piece of machinery or equipment. Also, HMIs can and frequently do offer data about the state and performance of this equipment.
HMIs can be digital or physical. Digital HMIs offer some advantages due to the ability to update and change controls without replacing or altering buttons, switches, and other physical inputs. Additionally, digital HMIs can easily display data, such as the current capacity of a storage tank or the operational state of a specific piece of machinery.
HMIs are intended to be used by the workers who directly control or oversee specific equipment. They are local, limited to a single machine or group of them, and focused on their performance and activity.
We’ll explore this more in the next section, but the high-level distinction in SCADA vs HMI is that HMIs are used for local control and insight into operations, while SCADA systems provide oversight and control across an entire production process, facility, or business.
Unlike SCADA systems, HMIs themselves don’t gather data or transmit it to a central database or other data storage system. HMIs are intended to provide local control over specific equipment. However, machines with HMIs are also generally connected to SCADA system, which does gather data and share it remotely, while also offering remote control capabilities.
HMI vs SCADA: Similarities and Differences
SCADA and HMI systems both offer capabilities to monitor and control devices. Both can offer valuable information and context to optimize the production process and avoid delays and other errors. So, what sets them apart?
It can help to think of HMI as a subset or component of a SCADA system. HMI is the frontline control that a machine operator or user interacts with while on the production floor or when otherwise in physical proximity to a specific machine or group of them. HMIs can and do display data and operational information,
SCADA is a larger-scale system overall that focuses more on data gathering and analysis for both historical analysis and real-time insight, on both the granular level and for production systems as a whole. HMI offers the same real-time insight for a specific machine but does not extend across the manufacturing workflow or throughout a company’s operations.
So, it can also help to think of HMI as operating on the “micro” level, while SCADA operates more on the “macro” level.
HMI is intended to be used by the employee or operator who is directly in control of or overseeing the operation of a specific piece of machinery or group of them. It offers insight into operations and control over that machine or machines, but its scope is clearly limited.
SCADA can remotely interact with and control production floor and field devices, especially when alarms and other warnings are triggered. However, SCADA is focused on the larger system and its overall performance. Another helpful differentiator: SCADA systems are generally used remotely, as opposed to by the direct operators of specific pieces of equipment.
A Comprehensive, Open-Source & Cost-Effective Approach to HMI & SCADA
Open Automation Software is proud to offer solutions that transport and transform operational data, building the most effective SCADA and HMI for organizations’ individual and unique needs.
Learn more about our proven and effective approach to industrial automation, a strategy that emphasizes accuracy, reliability, and security in data transport and use.
Download a trial of the OAS Platform to see what sets us apart.