Summary:
- IoT in manufacturing connects devices for real-time data collection, improving efficiency, reducing downtime, and enhancing productivity.
- Use cases include smart factories, predictive maintenance, supply chain optimization, and automated quality control.
- Benefits include smarter decision-making, enhanced safety, cost reduction, and scalability.
- The future of IoT involves AI integration, better cybersecurity, and faster data processing with edge computing.
The rise of the Internet of Things (IoT) is shaking things up across all industries, and manufacturing is no exception.
IoT in manufacturing is transforming how companies produce, monitor, and maintain their products. By connecting devices, sensors, and systems over the internet, manufacturers can gather real-time data, automate processes, and make smarter decisions faster.
In this post, we’ll explore some of the most valuable use cases and benefits of IoT in the manufacturing world and explore why it’s become such a game-changer.
Understanding IoT in Manufacturing
At its core, the Internet of Things (IoT) is all about connecting devices and systems to gather and share data. When it comes to manufacturing, this means using smart sensors, software, and other technologies to enhance production processes, improve efficiency, and minimize downtime.
Unlike traditional manufacturing setups, where machines operate in isolation, IoT in manufacturing enables seamless communication between equipment, systems, and even supply chains. This interconnectedness allows manufacturers to monitor operations in real time, spot inefficiencies early on, and make data-driven adjustments to optimize performance.
By integrating IoT technology, manufacturers can turn their facilities into intelligent environments where processes are streamlined, maintenance is proactive, and productivity gets a serious boost. It’s not just about upgrading machinery; it’s about creating a more responsive, efficient, and resilient manufacturing ecosystem.
IoT Use Cases in Manufacturing
Here are some IoT in manufacturing examples that are making a real difference:
Smart Factories
Smart factories are at the forefront of IoT adoption. By integrating IoT devices and systems, manufacturers can achieve real-time monitoring and automation of production lines.
Sensors continuously collect data on machine performance, environmental conditions, and operational efficiency, allowing manufacturers to adjust processes on the fly.
For example, if a particular machine shows signs of overheating, the system can automatically reduce its workload or alert maintenance teams before it leads to downtime.
Predictive Maintenance
Traditional maintenance schedules usually rely on rough estimates, which can mean either overdoing maintenance or dealing with expensive breakdowns. But with IoT in manufacturing, companies can take a smarter approach through predictive maintenance.
By using data from connected devices, they can predict when equipment needs attention before problems get out of hand. Sensors track things like temperature, vibration, and pressure to catch issues early. This proactive approach helps cut down on unexpected downtime, extend equipment lifespan, and save money on repair costs.
Solutions like our Alarm Logging & Notification software further enhance predictive maintenance by providing real-time alerts and detailed logs to keep operations running smoothly.
Supply Chain Optimization
The benefits of IoT aren’t limited to the factory floor. Implementing IoT technology across supply chains helps improve visibility and coordination from raw material sourcing to product delivery.
Real-time tracking of shipments, inventory monitoring, and logistics management are all enhanced by IoT systems. This greater transparency makes it easier to prevent delays, manage inventory levels, and ensure smoother, more reliable operations.
Quality Control and Production Efficiency
IoT devices play a critical role in improving quality control processes. By collecting and analyzing production data in real time, manufacturers can detect defects or inconsistencies early in the process. Automated systems can flag issues before they impact large batches of products, helping to maintain consistent quality standards.
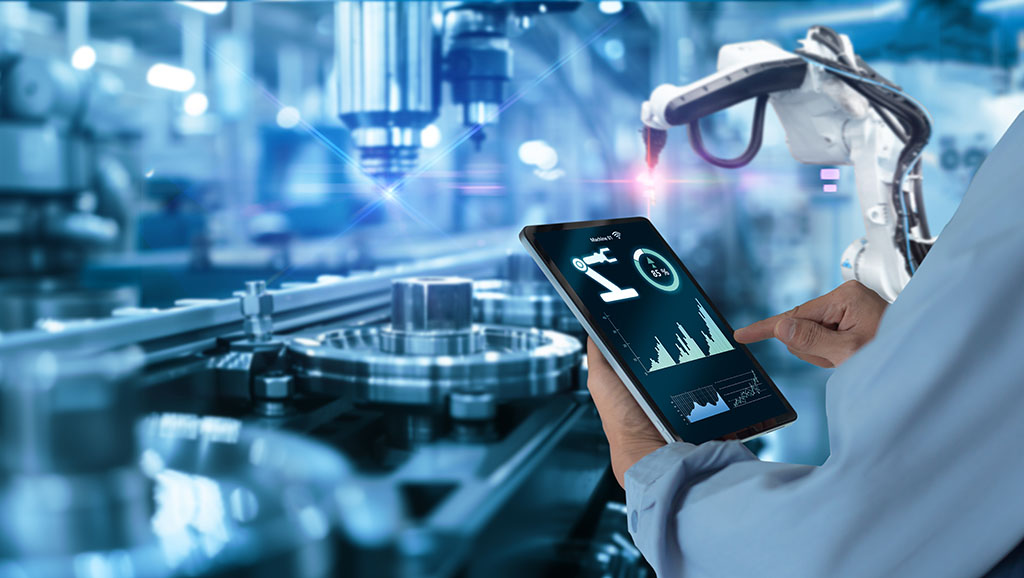
Benefits of IoT for the Manufacturing Industry
The true value of IoT in manufacturing goes beyond just making operations run smoother. Here are some of the standout benefits:
Smarter Decision-Making
IoT technology gives manufacturers real-time data that helps them make quick, informed decisions. Whether it’s adjusting production schedules or predicting inventory needs, having accurate data at your fingertips makes it easier to stay on top of changing demands and unexpected issues.
Tools like our Universal Data Connector make it easy to gather and integrate data from multiple devices, ensuring you always have accurate, real-time insights to drive better decisions.
Better Safety and Compliance
Safety is a big deal in manufacturing, and IoT helps keep workers protected by monitoring equipment conditions and environmental factors.
Automated alerts and predictive insights can catch potential hazards before they turn into bigger problems, making it easier to maintain a safe work environment and meet compliance standards.
Cutting Operational Costs
With predictive maintenance and more efficient workflows, IoT systems can significantly reduce operating expenses. Companies can avoid expensive repairs, cut energy use through optimized processes, and make better use of their resources where it matters most.
Flexibility and Scalability
IoT solutions are super flexible, making it easy for manufacturers to scale operations up or down as needed. From adding new devices and increasing production rates to expanding facilities, IoT tech supports growth without causing major disruptions.
Future of IoT in Manufacturing
The future of IoT in manufacturing looks incredibly promising, with new technologies and trends continually pushing the boundaries of what’s possible.
As IoT adoption grows, manufacturers are expected to see even greater improvements in efficiency, productivity, and overall performance. So, what’s on the horizon for IoT in manufacturing?
Increased AI and Machine Learning Integration
The combination of IoT, artificial intelligence (AI), and machine learning (ML) will take manufacturing to new heights. By using AI-powered analytics, manufacturers can gain deeper insights from IoT data, making predictive maintenance even more accurate and enabling smarter, real-time decision-making.
Better Cybersecurity Measures
With more devices getting connected, cybersecurity will continue to be a big focus.
Future IoT systems will include stronger security protocols and better data protection to keep operations safe and running smoothly, without the constant worry of breaches.
Faster Processing with Edge Computing
Edge computing is set to play a bigger role in IoT manufacturing. By processing data closer to where it’s being collected, manufacturers can cut down on delays and make real-time adjustments to improve efficiency and keep everything running like clockwork.
Making IoT Work for Your Manufacturing Needs
The impact of IoT in manufacturing is undeniable. From smart factories and predictive maintenance to advanced cybersecurity, IoT is reshaping how manufacturing processes are managed and optimized. As technology continues to evolve, the potential for IoT to drive even greater improvements in the manufacturing industry is only growing.
Ready to see what IoT can do for your manufacturing operations?
Discover how Open Automation Software can help you harness the power of IIoT to streamline your processes, boost efficiency, and gain better control over your industrial systems.
With OAS, you can easily visualize, manage, and integrate data from any device or platform to enhance your productivity and performance. Request a demo today to see how OAS can transform your manufacturing operations.