Summary:
- ICS controls machines and processes in real time, acting as the system’s “hands.”
- SCADA provides big-picture monitoring and management, serving as the “eyes.”
- ICS components (PLCs, RTUs) gather data, while SCADA processes and displays it.
- SCADA lets operators send commands, which ICS then executes.
- Together, SCADA and ICS improve efficiency, decision-making, monitoring, and safety.
Industrial automation powers modern manufacturing, energy, transportation, and more. At its core are two key systems: ICS (Industrial Control Systems) and SCADA (Supervisory Control and Data Acquisition). Though often mentioned together and sometimes used interchangeably, they serve distinct roles. Understanding ICS vs. SCADA is essential for engineers, system integrators, and OEMs navigating this space.
This article breaks down the differences between ICS and SCADA, explaining how they work together to streamline industrial automation.
What is ICS (Industrial Control Systems)?
ICS is the backbone of automated industrial operations. Think of it as the hands and muscles of an industrial process, directly managing and controlling physical equipment in real time.
Whether it’s regulating pipeline flow, adjusting conveyor speeds, or maintaining reactor temperatures, ICS keeps industrial environments running smoothly.
Key ICS components include:
- PLCs (Programmable Logic Controllers): The brains of many systems, PLCs process sensor data and send commands to machinery.
- RTUs (Remote Terminal Units): Used in widespread systems, RTUs gather data from remote sites and relay commands.
- HMIs (Human-Machine Interfaces): User-friendly dashboards that let operators monitor and control processes.
- Sensors: Measure key factors like temperature, pressure, and flow to inform system decisions.
- Actuators: Devices like valves, motors, and pumps that physically carry out control commands.
ICS isn’t just about monitoring—it actively controls operations in real time. In a factory, it directs robotic arms; in a power plant, it regulates turbines. Because ICS is so integral to operations, any failure or security breach can lead to downtime, equipment damage, or safety risks, making reliability and security top priorities.
What is SCADA (Supervisory Control and Data Acquisition)?
SCADA systems provide a big-picture view of industrial operations, acting as the eyes and strategic planner.
While ICS directly controls equipment in real time, SCADA monitors and manages entire systems, often across large areas. It doesn’t directly control processes but provides oversight and allows operators to make adjustments.
Core SCADA functions include:
- Data Acquisition: Collects data from PLCs, RTUs, and sensors for system-wide insights.
- Monitoring: Displays real-time data through dashboards for easy tracking and trend analysis.
- Supervisory Control: Lets operators issue commands like start/stop operations or setpoint changes.
- Alarming: Alerts operators to malfunctions, threshold breaches, or communication failures.
- Reporting: Logs historical data for trend analysis, optimization, and decision-making.
A SCADA system typically includes:
- Master Terminal Unit (MTU): The central hub that processes and displays data.
- RTUs/PLCs: Field devices that gather and transmit data.
- Communication Network: Links devices via radio, cellular, satellite, or wired connections.
SCADA has evolved from proprietary systems to modern, web-based, and cloud-enabled solutions. It plays a critical role in utilities, transportation, and manufacturing by providing the supervisory control needed for efficient, reliable operations.
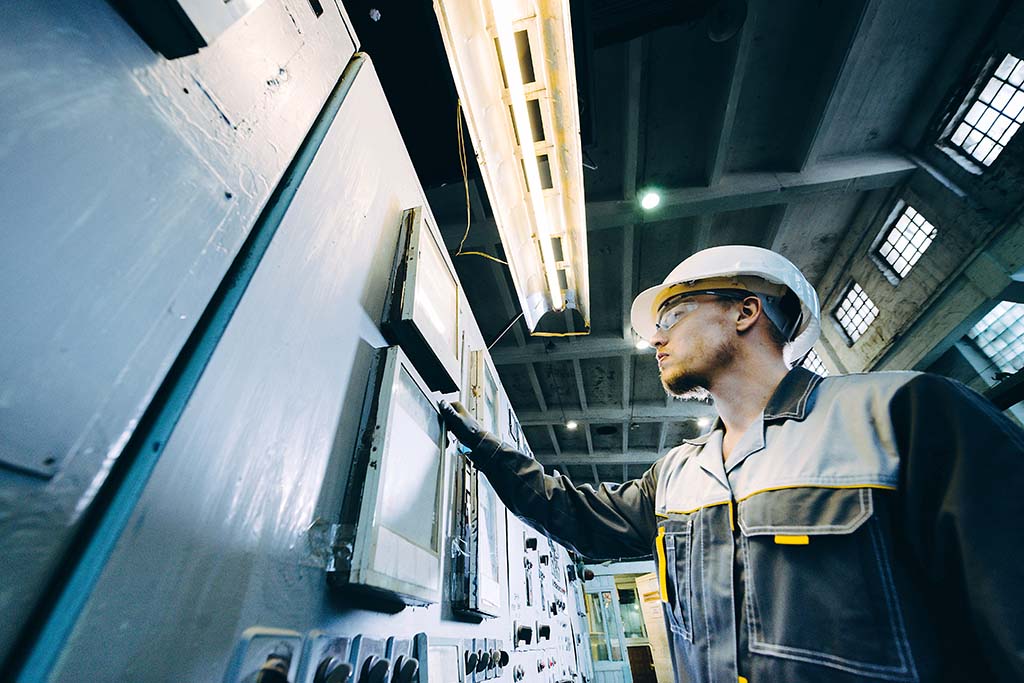
SCADA vs ICS: The Main Differences
The confusion around ICS and SCADA often comes from their close interaction, but understanding their differences is key to designing effective systems.
Here are the main differences:
ICS
ICS handles direct, real-time control of individual machines or processes. It makes instant decisions to keep equipment running smoothly—like controlling a robotic arm or managing a chemical reaction. ICS is the control.
SCADA
SCADA provides big-picture oversight of an entire operation. It gathers data from multiple ICSs, helping operators monitor and optimize large, distributed systems—like a pipeline network or a power grid. SCADA oversees the control.
Here are their scope and communication differences:
- ICS operates at a local level, controlling specific machines or processes with fast, real-time communication.
- SCADA manages widespread assets, using various communication methods that can handle delays and long-distance data transfers.
As you can see, SCADA and ICS complement each other. SCADA pulls data from ICS components, offering a centralized view for monitoring and decision-making.
While people sometimes use the terms interchangeably, knowing the difference between SCADA and ICS is crucial for optimizing industrial automation and ensuring efficient system performance.
How SCADA and ICS Work Together
While ICS and SCADA have distinct roles, they’re designed to work as a team, ensuring smooth and efficient operations.
ICS components (PLCs, RTUs) collect data from field devices and send it to SCADA, which processes the information, generates reports and alarms, and displays insights for operators.
Operators can then use SCADA to send commands, like adjusting setpoints or starting/stopping equipment, which ICS executes.
Key Benefits of SCADA & ICS Integration
- Improved Efficiency: A centralized view helps operators spot bottlenecks and optimize processes.
- Better Decision-Making: SCADA’s data insights support smarter operational choices.
- Enhanced Monitoring: Real-time tracking helps prevent downtime and costly failures.
- Optimized Control: Coordinated control of multiple ICS components streamlines operations.
- Increased Safety: Automated alerts help prevent accidents and equipment damage.
Real-World Examples
- Water Treatment: ICS controls pumps and valves, while SCADA monitors water levels and quality across the system.
- Power Grid: ICS manages substations and generators, while SCADA ensures grid stability and regulates power flow.
In every case, SCADA and ICS work together to keep industrial systems safe, efficient, and reliable.
A Powerful Partnership in Industrial Automation
Overall, it’s not really about ICS vs. SCADA—it’s about how they work together. ICS delivers precise, localized control, while SCADA ensures visibility and coordination across larger systems.
Recognizing this synergy is essential for building efficient, secure, and scalable industrial automation solutions. From manufacturing floors to power grids, ICS and SCADA power the modern industrial world.
Ready to maximize your industrial data? Discover how advanced software can help you integrate, visualize, and control your systems seamlessly.
Request a free demo from Open Automation Software today.