Summary:
- DCS (Distributed Control System) suits large, continuous processes like oil and gas and chemical manufacturing, offering high reliability, redundancy, and centralized control with optimized safety and precision.
- PLC (Programmable Logic Controller) is ideal for discrete manufacturing, machinery control, and smaller systems, providing flexibility, quick response, and lower costs.
- DCS uses centralized management of distributed controllers, while PLCs operate as standalone units or simpler networks.
- SCADA monitors and collects data from DCS and PLC systems, providing a unified view for decision-making.
- Choosing the Right System depends on process type, scale, budget, and control needs.
Choosing the right control system can feel like a big decision for any industrial operation. After all, it impacts everything from efficiency and reliability to overall costs. So, when it comes to DCS vs PLC, how do you know which one is the better fit?
Both Distributed Control Systems (DCS) and Programmable Logic Controllers (PLC) have their own strengths and are built for different kinds of applications. Understanding what sets them apart is the key to making the best choice for your operation.
In this post, we’ll break down how DCS and PLC systems work, where they excel, and which one might be the right match for your needs.
Understanding PLC and DCS Systems
Let’s explore what each system is designed to do and where they work best.
What is a Distributed Control System?
A Distributed Control System (DCS) is a computerized system built to automate and streamline industrial equipment used in large-scale processes. Its primary goal is to enhance safety, efficiency, and precision while minimizing risks to workers and the environment.
DCS systems are commonly used in industries like oil and gas, power generation, and chemical manufacturing. They work by connecting a network of controllers distributed throughout the facility, all managed from a central control room. This setup provides operators with real-time monitoring and control over complex processes, ensuring stability and consistency where it matters most.
For even better control and data integration, tools like our Universal Data Connector provide seamless connectivity across various platforms, making it easier to centralize data and enhance overall process management.
What is a Programmable Logic Controller?
A Programmable Logic Controller (PLC) is a highly reliable control system designed for managing specialized manufacturing processes and machinery control. Unlike DCS systems, which excel in continuous processes, PLCs are best suited for tasks that require quick responses and precise control, making them popular in industries like automotive, food processing, and packaging.
DCS Versus PLC: Key Differences
When it comes to PLC versus DCS both are used to control industrial processes, but their designs, applications, and strengths vary significantly.
Architecture and Control Approach
The way DCS and PLC systems are built is one of their biggest differences.
A DCS uses a decentralized structure with multiple controllers spread throughout a facility, all connected to a central control room. This setup offers a streamlined approach to managing large, complex processes, especially those that run continuously.
Meanwhile, a PLC is usually a standalone controller, working independently or as part of a broader network. It relies on programmed logic to monitor inputs and generate outputs, making it perfect for discrete manufacturing and tasks that need fast, precise control.
While PLCs can be networked together for more complex control, their architecture is generally simpler and more straightforward than what you’d find with a DCS.
To enhance system integration and data logging across DCS and PLC systems, implementing reliable data historian software can be a game-changer.
Scalability and Flexibility
Another big difference between distributed control systems vs PLC systems is scalability.
DCS systems are built to handle complex, large-scale processes where monitoring, control, and redundancy are critical. They excel at providing a unified approach to managing continuous operations.
On the flip side, PLCs are all about flexibility. They’re easy to modify, expand, or reprogram as your needs change, making them a great option for smaller systems or projects that need frequent updates or adjustments.
Cost and Implementation
Cost is another area where DCS and PLC systems differ. DCS systems typically come with higher upfront costs because of their complexity and the need for centralized control rooms. But for industries where precision, safety, and integration matter most, that investment often pays off.
PLCs, being simpler and more modular, are generally more cost-effective. They are easier to install, program, and maintain, which makes them a popular choice for companies looking for practical solutions at a lower price point.
Use Cases and Best Applications
Choosing between DCS vs PLC often comes down to what you need the system to do.
- DCS systems shine in industries where continuous or batch processes are the norm, and automation, redundancy, and safety are top priorities.
- PLCs work best in discrete manufacturing, machinery control, and processes where quick responses are crucial.
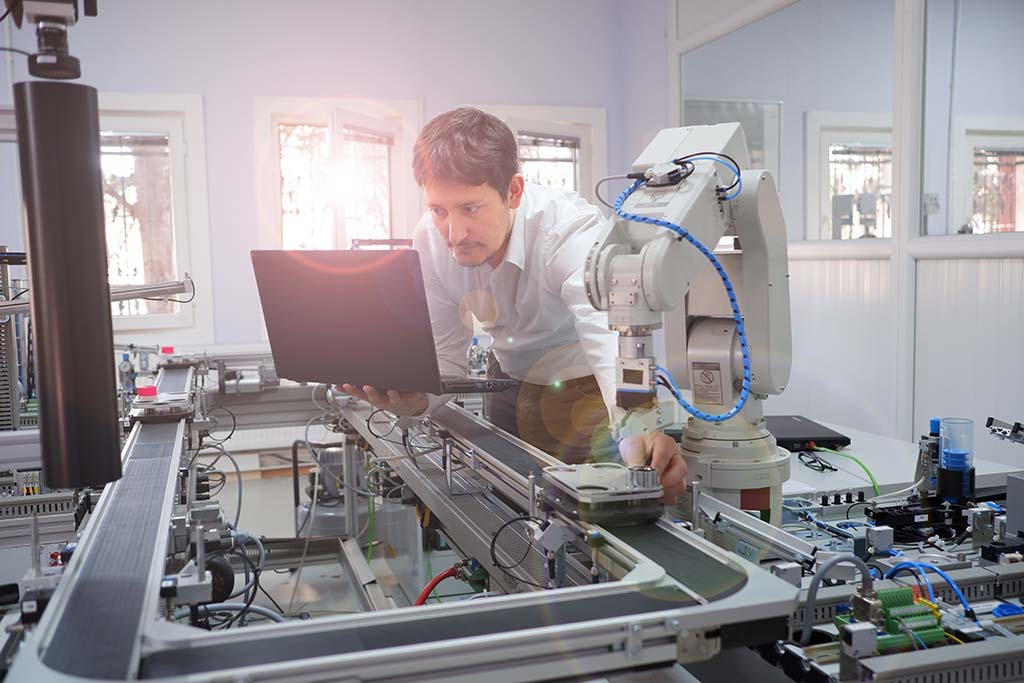
The Differences Between DCS, PLC, and SCADA
So far, we’ve covered the basics of DCS and PLC systems, but what about SCADA? Understanding how SCADA fits into the DCS vs PLC discussion is key to getting a full picture of industrial control systems.
What is SCADA?
SCADA (Supervisory Control and Data Acquisition) is a software-based system used to monitor and control industrial processes remotely.
Unlike DCS and PLC systems, which are more about direct control of equipment, SCADA is designed to collect data from multiple sources, process it, and present it to operators through user-friendly interfaces. It’s all about providing a bird’s-eye view of operations so that decisions can be made quickly and effectively.
How SCADA Relates to DCS and PLC Systems
SCADA often works alongside both DCS and PLC systems.
With DCS systems, SCADA can enhance monitoring capabilities by gathering and visualizing data from distributed controllers. Since DCS already provides centralized control, SCADA typically plays a supporting role by providing enhanced visualization and data management.
With PLCs, SCADA serves as the supervisory layer that ties multiple PLCs together, providing a unified platform for monitoring and managing various processes. This combination is common in industries where discrete processes or batch manufacturing are the focus.
Is SCADA a PLC or a DCS?
Neither. SCADA is more like an overarching system that sits on top of DCS and PLC systems. While it doesn’t control processes directly, it collects data from both DCS and PLC systems, allowing operators to visualize and manage everything from a central interface.
Choosing the Right System for Your Business
Choosing between DCS vs PLC comes down to your specific needs, processes, and budget.
For large-scale, continuous operations that demand centralized control, precision, and redundancy, a DCS is often the best fit. It’s a reliable choice for industries like oil and gas, power generation, and chemical manufacturing.
If you’re focused on discrete manufacturing, machinery control, or smaller systems requiring quick responses and flexibility, a PLC is usually the way to go. Its simplicity, cost-effectiveness, and adaptability make it ideal for industries where scalability and responsiveness are essential.
Ready to optimize your industrial automation?
Open Automation Software (OAS) offers the tools you need to visualize, control, and integrate data across any industrial device or platform. Request a demo with OAS today and discover powerful IIoT solutions built for your needs.